Which electroplating color is easiest to change color?
1. White steel: electroplated stainless steel, which is the most common white electroplating material;
2. Light gold, frosted gold: gold, mostly using 14K gold plating;
3. Rose gold: Rose K gold electroplating, suitable for young and fashionable consumers;
4. Light silver: Electroplated silver, the purest of all whites, is more common in earrings and brooches. It is hypoallergenic and unlike sterling silver which easily oxidizes and turns black, it ensures a pure and durable color;
5. Gun color: similar to the color of the surface of a gun barrel, black and shiny, stable in nature, and least likely to change color;
6. Oxidized silver: Pure silver easily turns black in the air. After oxidation treatment, its properties become more stable, and its color is more ancient and soft, giving it a retro look and feel;
7. Bronze oxidation: red, ancient color;
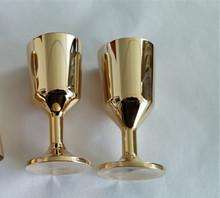
9. Platinum: electroplated platinum. It is the electroplating with the best color and quality inside white, and is usually electroplated on the surface of copper materials.
Causes and solutions of graying
White fog after nickel plating usually occurs together with blackening of deep holes and other places. It is because the nickel plating solution is contaminated by metal impurities and organic impurities. Metal impurities such as zinc and copper will cause the coating in the low current area to become dark and black; too many organic impurities, improper use of additives or imbalance (see note below) will cause the nickel plating layer to become foggy and white. The solution is to clean the plating solution. deal with. The treatment process is as follows;
(1) Take out the anode, add 5ml/l of impurity removal water, heat to 60-70 degrees C, and mix in air for 2 hours. (You don`t need to add it if you don`t have a reliable impurity remover on hand).
(2) If there are many organic impurities, first add 3-5ml/lr of 30% hydrogen peroxide for treatment and mix with air for 3 hours.
(3) Add 3-5g/l powdered activity under constant stirring, continue air stirring for 2 hours, turn off stirring and let stand for 4 hours, filter, and clean the tank at the same time.
(4) Clean and maintain the anode hanging back.
(5) Use a nickel-plated corrugated iron plate as the cathode and conduct electrolysis at a current density of 0.5-0.1 A/square decimeter until the surface of the corrugated plate turns gray-white (similar to the color of dark nickel). This process takes about 4 -12 hours, longer if there are too many impurities. During electrolysis, air mixing or cathode movement must be turned on to improve the treatment effect.
(6) Analyze and adjust various parameters, add some additives and humidifiers lost during processing, and conduct Hall cell experiments if necessary. After passing the test, trial plating can be started.